
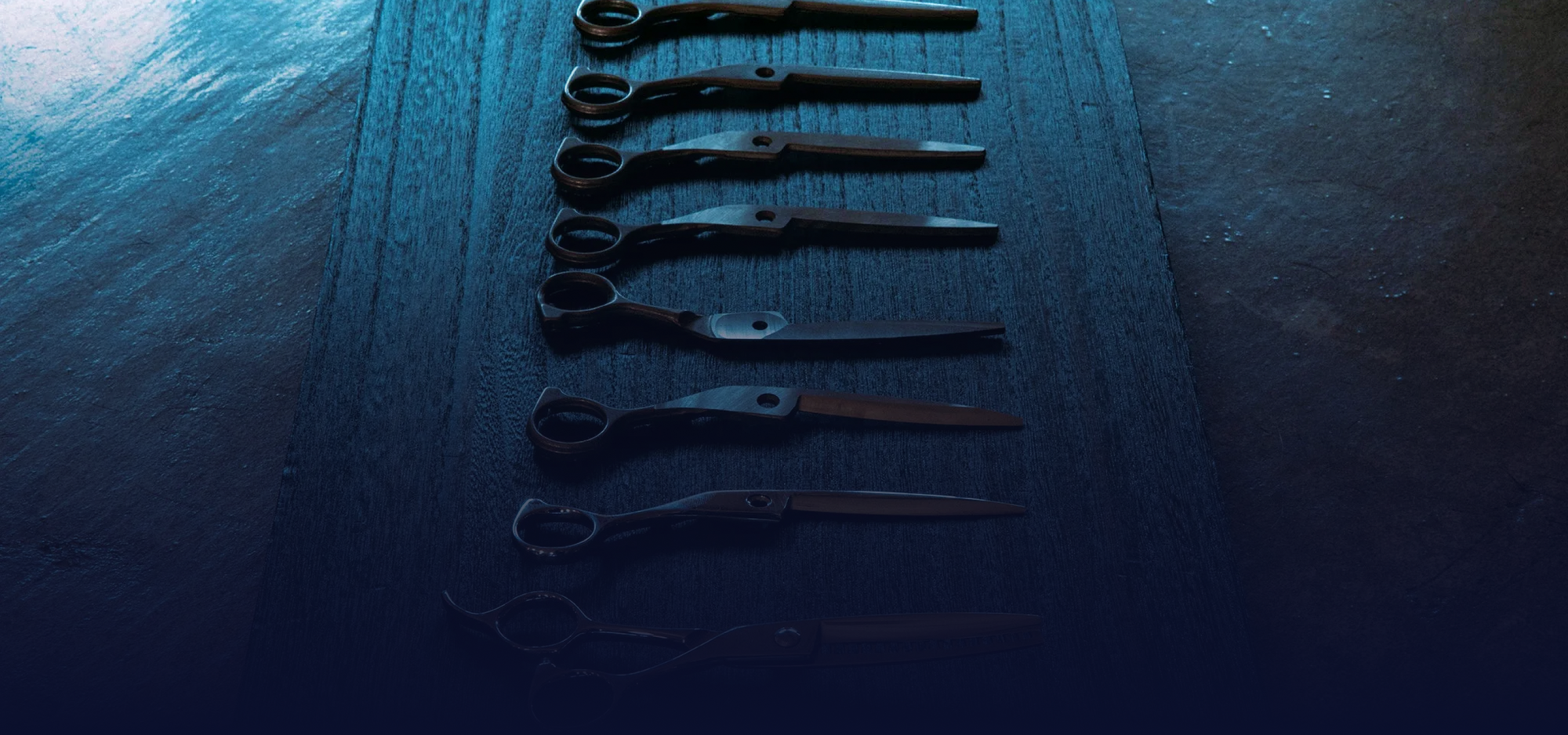
Our Commitment To Excellence
Why You Should Invest in Good Shears
Using dull shears can lead to “clamping” which can cause damaging of hair follicles. This kind of “blunt force cutting” creates split ends and entry points for chemicals which can easily damage the hair. We encourage that professionals at any level of their careers to do your research to choose the best option for you.
Our Dedication
ATO dedicates it’s craftmanship to producing controlled production which maximizes the shears durability. We take great pride in working with our factory in Niigata, Japan to provide the shears with the highest degree of precision and reliability.
Please note that we are not a mass-producing manufacturer. We operate in partnership with our factory in Niigata, Japan while producing about 100 products a month. Every shear that is produced through ATO has had over 300 hours of hand crafting from forging, molding, to sharpening with our master crafters.
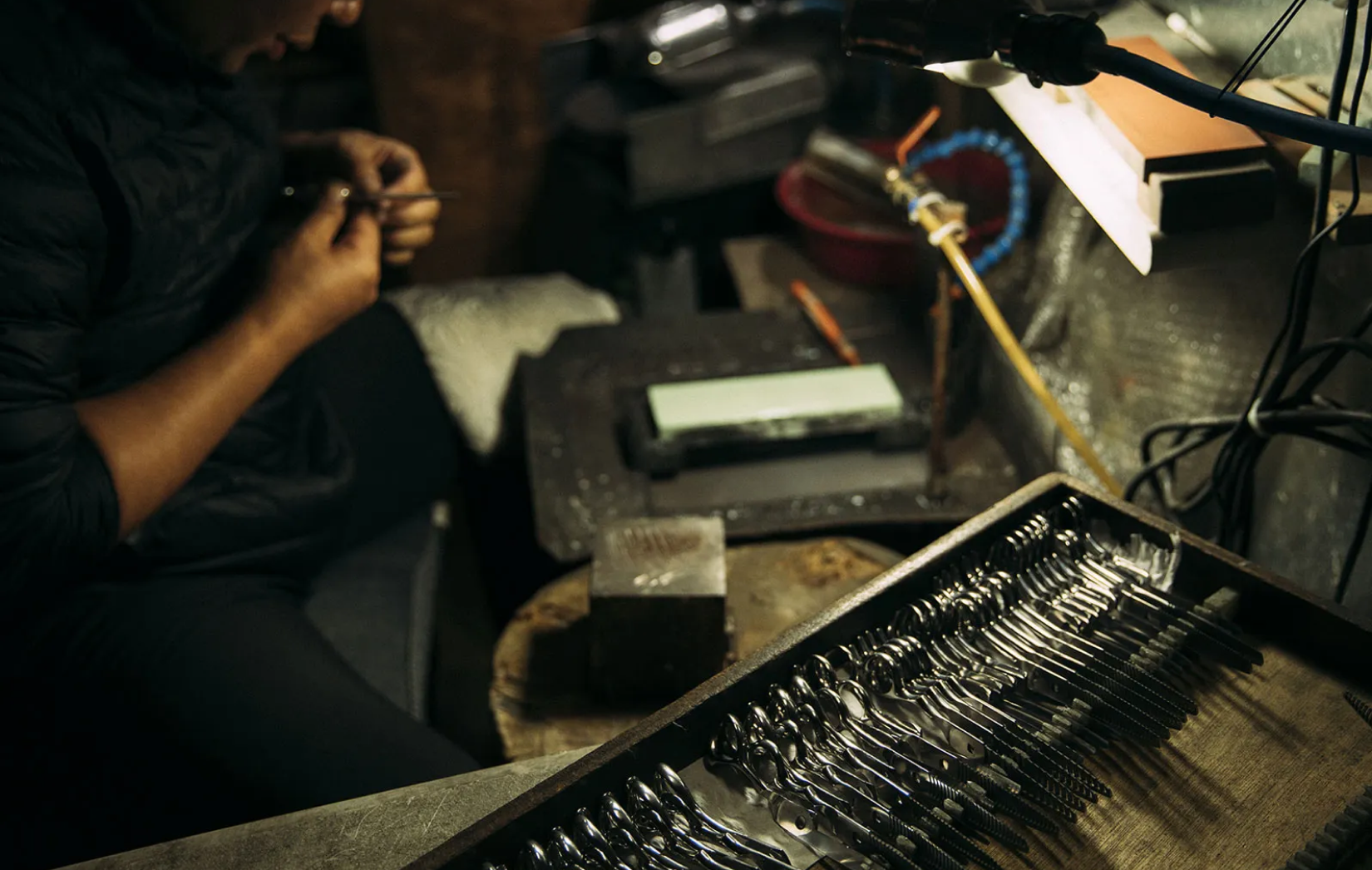
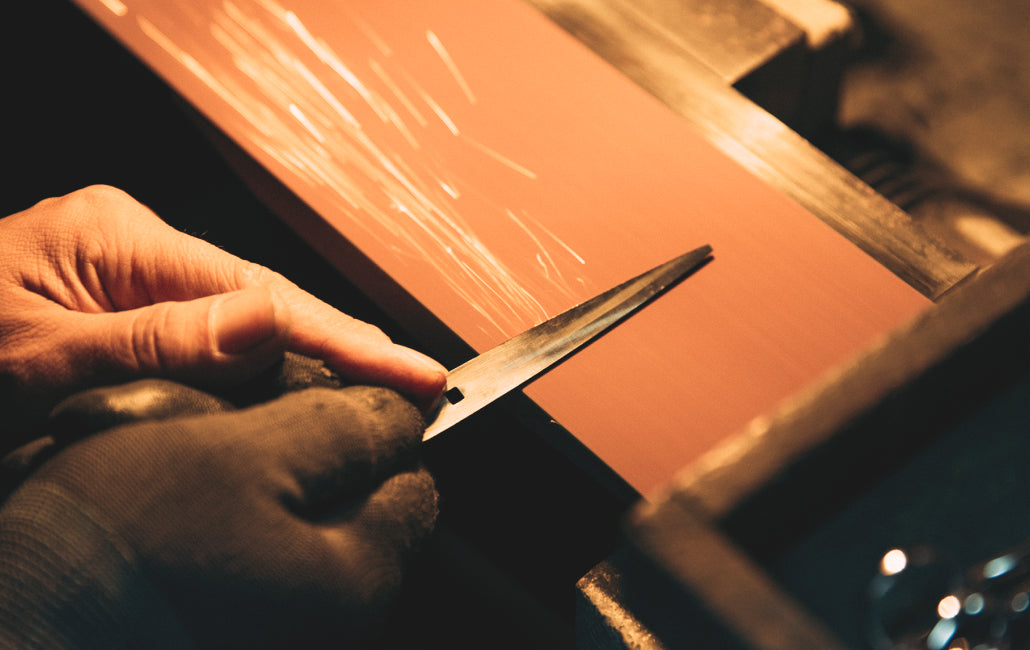

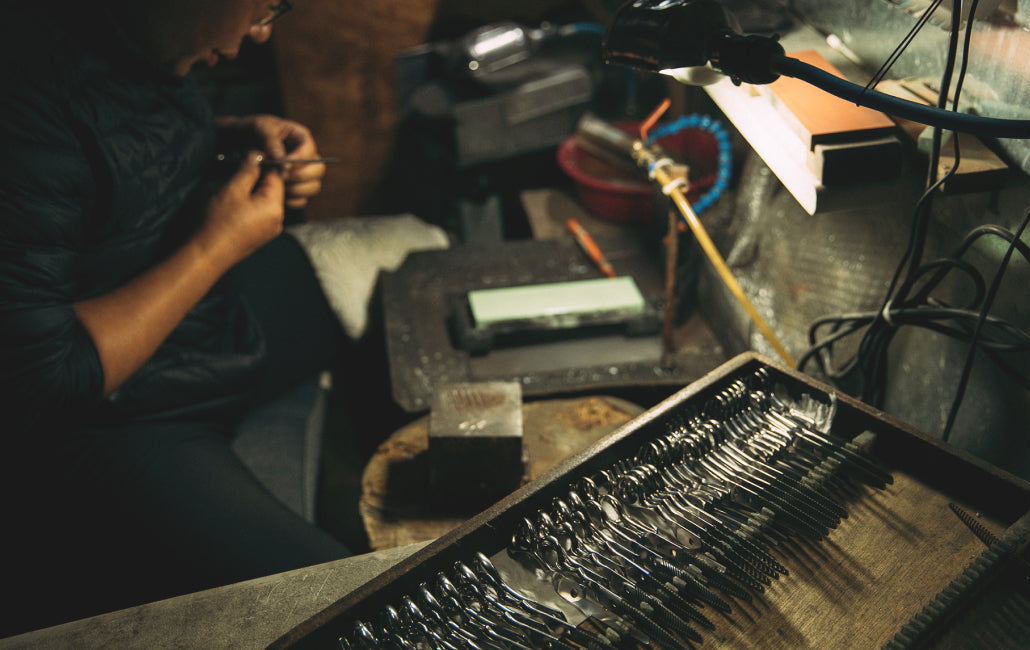